EHS personnel refers to individuals responsible for managing environmental, health, and safety (EHS) issues within an organization. These professionals work to ensure that their organization complies with all relevant regulations and standards related to environmental protection, occupational safety, and employee health for that the following 10 mistakes every EHS personnel MUST avoid
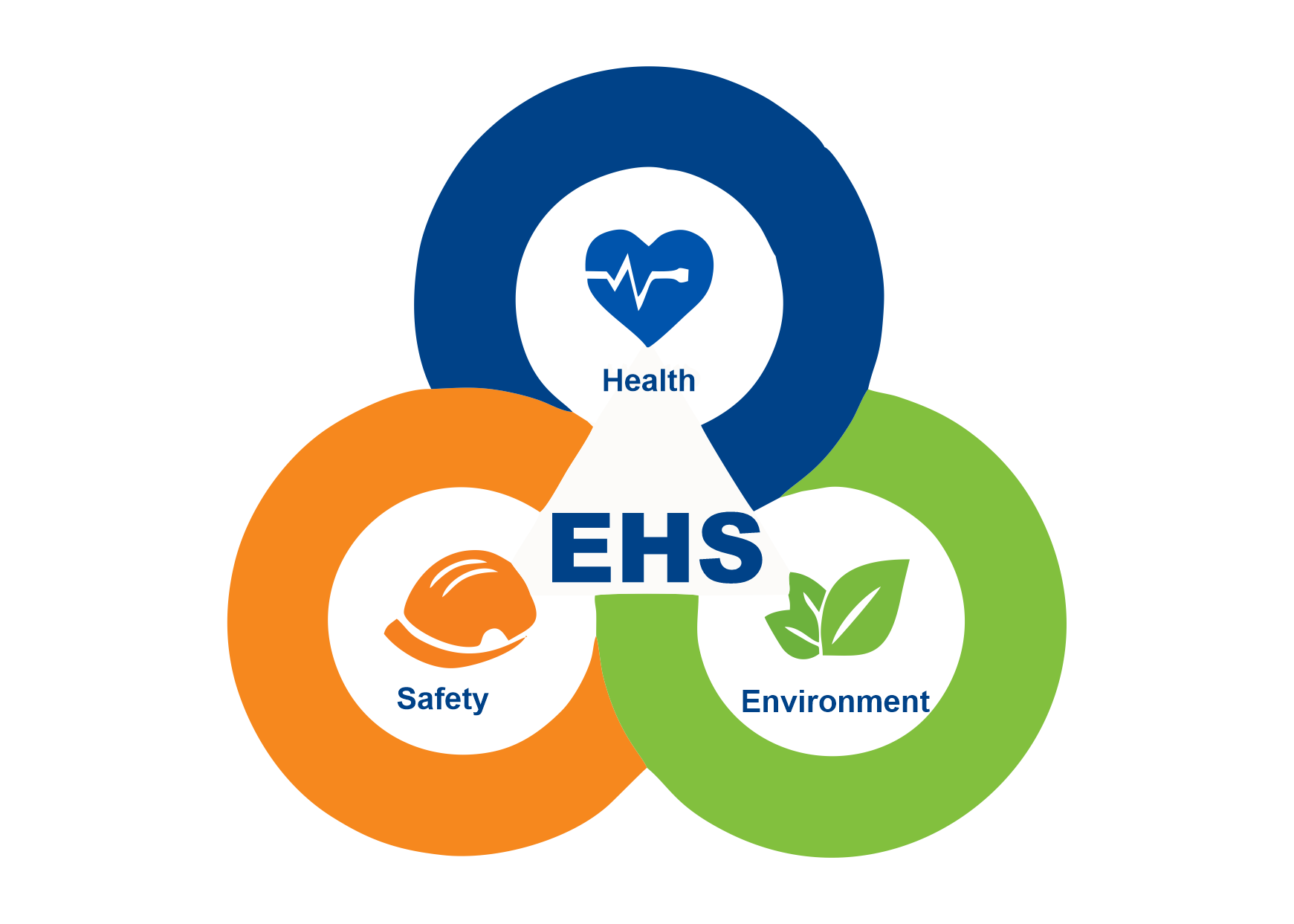
EHS personnel may have a variety of job titles, including EHS manager, safety coordinator, environmental compliance specialist, industrial hygienist, and occupational health and safety specialist. Their responsibilities may include developing and implementing safety policies and procedures, conducting safety training, conducting safety inspections and audits, monitoring and analyzing safety data, and managing environmental compliance.
EHS personnel may work in a variety of industries, including manufacturing, construction, healthcare, and transportation. They play a critical role in ensuring that organizations operate in a safe and environmentally responsible manner, protecting the health and well-being of employees and the surrounding community.
Here are 10 mistakes that EHS personnel MUST avoid:
- Not staying up-to-date with EHS regulations and laws: As an EHS professional, it is essential to stay current with EHS laws and regulations. This can help you ensure that your organization is in compliance with all applicable regulations.
- Ignoring potential hazards: Failing to identify and address potential hazards can lead to accidents and injuries. Make sure you perform regular hazard assessments and take necessary measures to mitigate risks.
- Not properly training employees: Without proper training, employees may not understand the potential risks associated with their jobs or know how to use safety equipment. Make sure all employees receive thorough training on EHS policies and procedures.
- Failing to communicate EHS policies: Communication is critical in ensuring that all employees understand the importance of EHS policies. Make sure that your organization’s EHS policies are communicated effectively and regularly.
- Not providing adequate personal protective equipment (PPE): Employees must have access to appropriate PPE to protect themselves from workplace hazards. Make sure that PPE is provided and regularly checked to ensure it is in good condition.
- Overlooking ergonomic issues: Ergonomic issues such as improper workstation setup or repetitive motion injuries can cause significant health problems. Make sure that ergonomic assessments are performed, and necessary measures are taken to address issues.
- Not conducting regular safety audits: Regular safety audits help to identify potential hazards and ensure that EHS policies are being followed. Make sure that your organization performs regular safety audits.
- Failing to investigate incidents: Incidents and accidents should be investigated to determine the root cause and prevent future occurrences. Make sure that all incidents are thoroughly investigated.
- Not involving employees in EHS initiatives: Employees can be a valuable resource when it comes to identifying potential hazards and suggesting improvements to EHS policies. Make sure that employees are involved in EHS initiatives and that their input is valued.
- Not prioritizing EHS: EHS should be a top priority in any organization. Failing to prioritize EHS can lead to accidents, injuries, and even fatalities. Make sure that EHS is taken seriously and that appropriate resources are allocated to ensure a safe and healthy workplace.